- To hit its net zero targets, the world is relying on a controversial technology pioneered by the fossil fuel industry. It’s going to cost $4.5 trillion this decade.

By Stephen Stapczynski
Get within a few dozen meters of one of the world’s biggest carbon capture projects on Australia’s remote Barrow Island, and normal conversation quickly becomes impossible.
Emanating from the dense maze of pipes and towers the size of a city block is the roar of carbon dioxide escaping into the atmosphere — exactly what Chevron Corp.’s ambitious $2.1 billion system was supposed to stop.
The Gorgon project sits 60 kilometers (37 miles) off the northwest coast of Australia next to a vast gas field. Chevron received approval to develop the site into a major liquefied natural gas export facility on the basis they could capture and store 80% of the CO2 mixed in with the fuel, instead of releasing it.
Since LNG production started in 2016, they mostly haven’t. Mitigation operations started late, ran in spurts and were beset with technical issues. Right now, while the facility is successfully capturing CO2, it is only storing 1.6 million tons per year, under half its 4 million tons capacity, after struggling to inject the gas into the ground reliably.
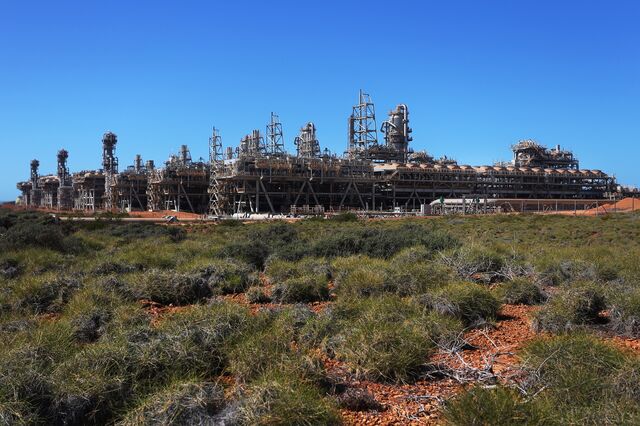
Carbon capture and storage is one of the most contentious solutions in the drive to cut greenhouse gas emissions. In the last three decades, according to BloombergNEF data, governments and corporations have poured over $83 billion into projects. Last year the technology captured just 0.1% of global emissions.
Yet enthusiasm at Chevron, the second-biggest US oil and gas producer, is undimmed. It’s planning to press on, spending even more money on the divisive technology, both at Gorgon and elsewhere.
“We gotta get started and really get going,” said Chris Powers, vice president of carbon capture, utilization and storage at Chevron’s New Energies unit and the company veteran charged with getting Gorgon back on track. “These are multi-year projects that are gonna take, many, many, many millions of dollars to progress.”

One of the biggest problems is that unlike technologies such as solar, which have reached mass scale and are now close to drop-in solutions, CCS is still a bespoke suite of processes. It’s expensive, site-specific and has needed custom engineering virtually everywhere it’s been tried.
Many environmentalists say the technology should be abandoned, arguing it is simply a way for the fossil fuel industry to justify its continued existence and to avoid having to write down the value of its assets.
Yet CCS is also one of the world’s last best hopes to limit dangerous warming.
The world is filled with high-emission, high-cost infrastructure like power stations and factories that cannot be easily scrapped in favor of green alternatives. In some cases, because the assets were recently built in cash-strapped countries who can’t afford to decommission them. In others, because there isn’t yet a commercially viable way for industries like cement and steel smelting to decarbonize. If CCS technology can be retrofitted, the world gains valuable time.
That’s why climate scientists from the likes of the Intergovernmental Panel on Climate Change – hardly apologists for Big Oil – say CSS is an unavoidable necessity.

Roughly another 300 facilities of similar size to Gorgon need to be up and running by 2030 to keep the world on track for net-zero emissions by the middle of this century, according to Bloomberg News calculations based on scenario planning from the International Energy Agency.
The Carbon Capture Wall
A huge increase in global capacity is needed to achieve net-zero emissions

But after decades of slow progress, time is quickly running out. As projects normally take five to seven years from announcement to commissioning, that gives the industry just two years to build trust in CCS and significantly scale-up investment. Some $4.5 trillion is needed by 2030, according to BloombergNEF.
Gorgon, incongruously perched on a nature reserve of red dirt, scrappy vegetation and rare marsupials, is one of the projects that simply must hit its targets to convince skeptics that the technology is viable.
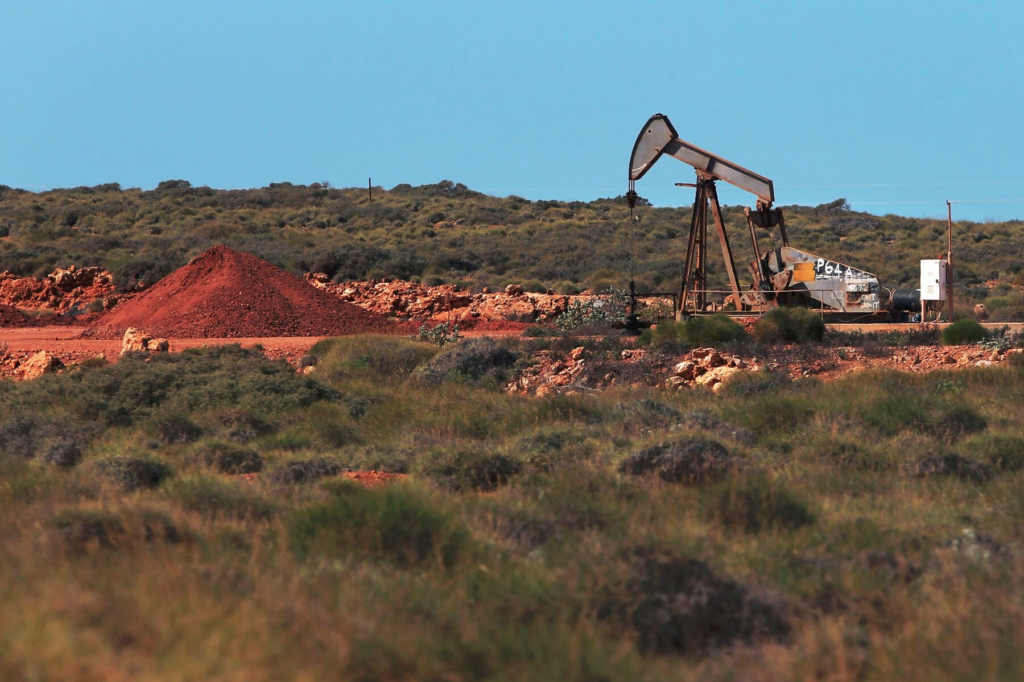
In the early-1970s Chevron made history by injecting leftover CO2 captured from an oil field to produce more fuel at scale. Usually, the gas would have been vented but instead engineers used it like soap to squeeze out extra oil.
For the next 30 years this was the main application of carbon capture: not constraining greenhouse gas emissions but producing even more fossil fuels. Then as concerns about global warming gathered pace, the industry started to experiment with using CCS to operate refineries and gas fields with a lower carbon footprint.
It’s been a frustrating journey. Some 78% of large-scale demonstration and pilot projects initiated between 1995 to 2018 have been canceled or put on hold, according to a 2021 study. High costs were a key issue.
The IEA says that currently 40 projects globally are capturing carbon at a commercial level. That’s in sharp contrast to the exponential increase in wind and solar installations.
One project the industry often touts as a success is Quest in Scotford, Canada, operated by Shell Plc. It handles emissions from a facility that creates hydrogen to upgrade bitumen from oil sands fields, allowing the thick fuel to be refined into products like gasoline.

Built on time and under budget, it’s operated near its full 1 million tons a year capacity for the first seven years of operation – although the actual volume of avoided emissions is lower because the site generates other pollution that is not captured.

Learning from Quest’s construction, Shell hopes to use modularized designs and existing technologies in future endeavors, reducing the need for heavily engineered systems tailored for individual projects. That approach could also help cut costs.
“We don’t talk about CCS, we are doing CCS,” said Zoe Yujnovich, head of Shell’s integrated gas and upstream business, which is responsible for exploration and production. CCS is “absolutely critical for my business.”
Quest is also one of the projects that Chevron’s Powers, 43, a jovial chemical engineer by training, is looking to for lessons. Weeks before he started the role, Chevron announced that it aims to capture and offset 25 million tons per year by 2030, equivalent to about six Gorgons.
Powers — like much of the wider oil and gas industry — says making CCS work is non-negotiable if the world wants to maintain its current style of living.
“I just fundamentally don’t believe that society is willing to sort of go back to the Old West or Stone Age,” said Powers. “We’re doing an important thing here to feed the growing demand of energy in the world.”
Powers is a third-generation oil man. His grandfather did construction work on refineries and chemical plants. His father was a chemical engineer involved in the processing of hydrocarbons. “And now we’re capturing CO2 that’s critical to the quality of life that we all have, and putting it back to the ground — that’s the personal story I tell folks, it’s sort of full cycle.”
Most CCS projects share some core elements. They use chemical solvents to remove CO2 in towers; pipes to cool, heat and transport the gas; and then pressurized systems to store it, often within hollow natural caverns that were once home to fossil fuels.

Engineering in remote locations always requires some degree of ingenuity. On Barrow Island, for example, the equipment that flares gas — an approach used in emergencies to relieve dangerous pressure build-ups — had to be separated to be further inland and surrounded by massive black walls so that turtles wouldn’t think it’s the moon and use it to navigate the island.
Yet when it comes to CCS, the degree of customization required is extreme.
At Gorgon back in 2017, trace amounts of water in the pipes transporting the CO2 triggered an acidic reaction that was rapidly eroding the equipment. Chevron had to stop all CO2 transport until engineers finally decided they could fix the problem by installing machines that dehydrated the CO2. That delayed start-up.
“This is not a cookie cutter technology,” said Christina Ng, an analyst at the Institute for Energy Economics and Financial Analysis, a non-profit which advocates for a transition away from fossil fuels. “It is so specific, it is so sensitive to the location which it is put in, it cannot be replicated easily to just anywhere.”
Now, issues with water and pressure management when injecting CO2 are plaguing the facility. Solutions being reviewed include removing and transferring water into another reservoir nearby, allowing CO2 to be injected at a higher rate. The price tag is still being determined.
In the meantime, to make-up for the shortfall, Chevron must buy millions of tons of carbon offsets, including from a market that’s been criticized for failing to abate greenhouse gas emissions.
Despite the industry’s difficulties, all around the world governments are doubling down. President Joe Biden’s US Inflation Reduction Act contains the provision for tax credits which could cover the cost of building and operating carbon capture facilities. The UK is committing as much as £20 billion to subsidize CCS over the next two decades, while the European Union aims to inject 50 million tons a year by 2030 — a 66% increase on what is currently planned.
G-20 leaders gathering in New Delhi agreed to support the expansion of abatement technologies, reflecting a wider retreat from ambitions to rapidly phase out fossil fuels. This year’s COP28 United Nations climate summit in the United Arab Emirates will also advocate strongly for the technology. “In any realistic scenario that gets us to net zero, carbon capture technology will have a role to play,” COP28 President Sultan Al Jaber said in a May speech. “Without it, the math just doesn’t add up.”
QuickTake: How Carbon Capture Is Getting New Life With USHelp
And in Japan, CCS is the centerpiece of its transition plan. Instead of pivoting quickly to cheaper wind and solar generation like most of its G7 peers to decarbonize its power sector, authorities are counting on the technology to extend the life and cut emissions from its massive coal and gas plants.
By 2050, it plans to have the equivalent of as many as 60 Gorgons operational. It’s a high-risk strategy, because any hiccups threaten to derail efforts to curb pollution in the second half of the century.
Key to its hopes for a breakthrough are innovation hubs like Omuta, on the southern island of Kyushu. Once home to one of Japan’s oldest coal mines, for over a decade it’s housed a team of Toshiba Corp. engineers. Currently, they are trying to couple CCS with the next door Mikawa biomass plant.
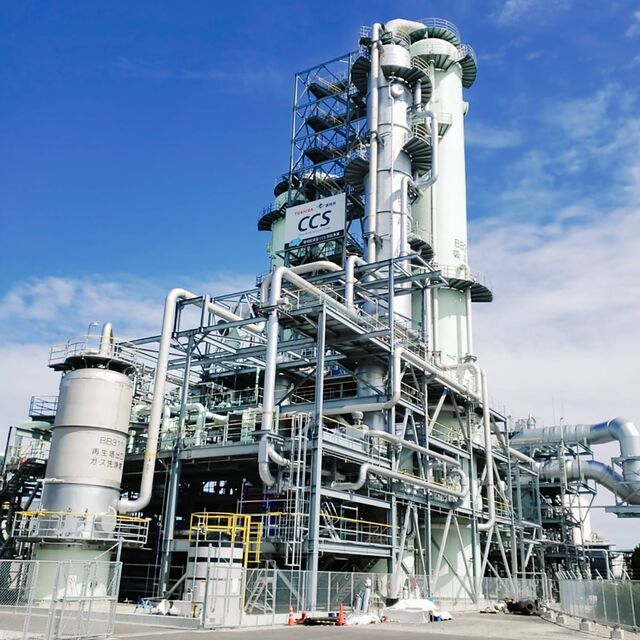
Since the fuel at Mikawa is renewable — it burns palm kernel shells — capturing the emissions would make it carbon negative, at least in theory. The facility runs for short testing periods during the frigid winter and blistering hot summer, providing vital datapoints for Toshiba and Japan’s nascent CCS industry.

The project is so experimental small metal placards hang off every inch of the plant to let engineers know exactly what each piece does. They chime every time the wind blows.
Toshiba and its partners plan to liquefy the CO2. Japan is looking to potentially send CO2 to places like Australia, which has more room for storage.
For skeptics, CCS is nothing more than a fantasy get-out-of-jail-free card for polluters, sucking up cash that would be better deployed elsewhere.
“It’s great propaganda in the sense that it gives the user the notion that we can keep burning fossil fuels and not have so many emissions,” said Charles Harvey, professor of civil and environmental engineering at the Massachusetts Institute of Technology. “Put the subsidies into the technologies that are good, that work, that are efficient.”
And it’s those who stand to gain most who are often the strongest proponents. Toshiba, for example, is also a large supplier of turbines for fossil fuel power plants. Plus CCS is one of the few ways to reconcile environmental targets with the decision by a number of large oil and gas producers to cut output at a slower rate than previously planned in the aftermath of Russia’s invasion of Ukraine.

Barrow Island is dotted with oil wells drilled in previous decades. Many are still oscillating up and down today, producing a tiny bit of crude next to bulbous termite hills and the native spectacled hare-wallabies.
The natural gas the island is now focused on is in high demand as a so-called transition fuel as Asian nations seek to move away from dirtier coal. But Australia is bearing the carbon cost nonetheless: the Gorgon project was the country’s largest polluter during the year through June 2022, according to the latest available data from the regulator.
For all the site’s setbacks, there are successes that give the company optimism. Underneath the dusty red earth, pipes are actually transporting some CO2, captured and condensed to a supercritical state, roughly two kilometers underground.
At the three injection sites there is no ear-wrenching racket of equipment, or even a modest hum. You’d only know the wells are operating as intended by the constantly changing numbers on small digital monitors.
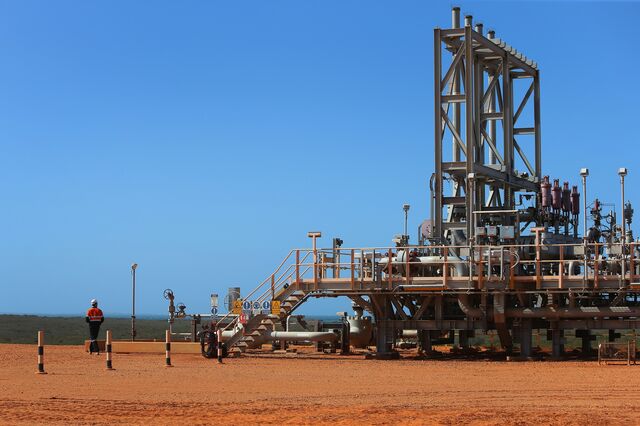
“We’re about to put significantly more dollars on the ground to take the capacity up to our desired optimal rate,” said Chevron’s Powers. “Although we’re not fully where we wanna be, we can actually point to and say we are operating a project that is capturing the CO2.”
That sentiment sums up the carbon capture industry. For decades, the industry has had something to point at to say the technology works. Yet despite these accomplishments, it’s not currently operating at a large enough scale to make a meaningful impact in slowing down climate change.
Edited by Emily Cadman and David Stringer
Photo editing by Yuki Tanaka and Eugene Reznik
With assistance from Sheryl Tian Tong Lee, Aaron Clark and Akshat Rathi
______________________________________________________________
Stephen Stapczynski is Bloomberg @Business senior reporter covering energy & commodities in Singapore.
Bloomberg.com 09 15 2023